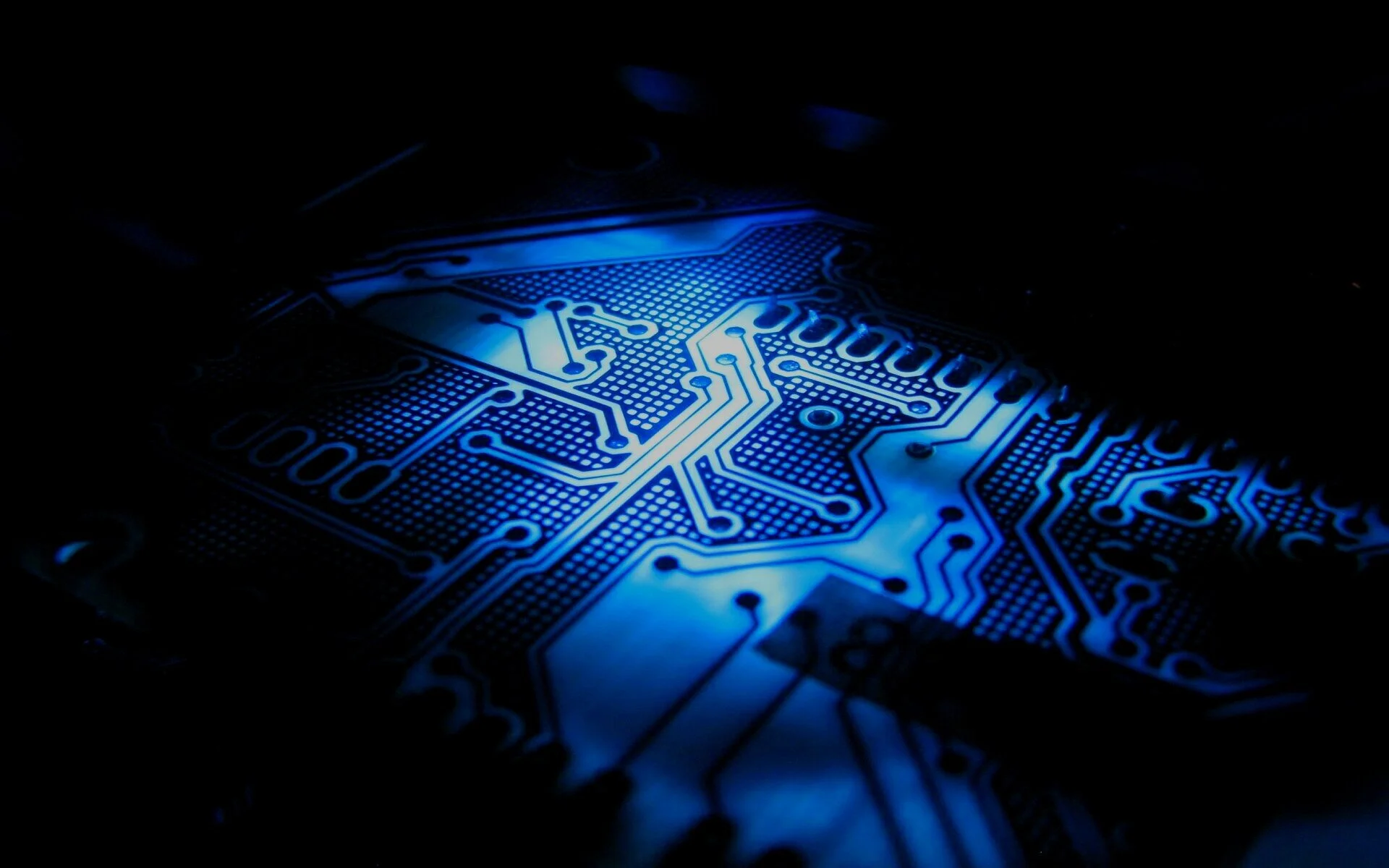
Exolv (verb): To set free lab-grown diamond technologies that make the future possible today
A DCCVD diamond reactor to revolutionize the industry
Headquartered near Salt Lake City, Utah and nestled beneath the beautiful mountains of the Wasatch Front, Exolv focuses on developing world-leading lab-grown diamond reactors and processes for gemstone and technology applications. This system produces high-quality single-crystal and polycrystalline diamond with the largest growth area in the industry at 130 mm diameter.
The direct current chemical vapor deposition (DCCVD) reactor provides numerous benefits over competing systems, ranging from production volume, ease of use, thermal consistency, process control, and capital and operating cost, while experiencing success with consistent, high-quality growth.
Simply said, there is no better reactor for diamond production, whatever your needs. Contact us today for more information.
Contact us.
Ask any questions, explore any possibilities.
Areas of Experience
Reactors
The most critical aspect of any diamond growth is the reactor. Without a good system, nothing else is possible. This is where Exolv excels, using a proprietary and patent pending system with the largest deposition area in the industry. The 130 mm diameter growth area provides uniform, high-quality growth, far beyond any system available.
Process
With a great reactor it is now possible to develop the critically important process. Unlike other diamond equipment suppliers, Exolv can provide a process capable of high-quality single-crystal and polycrystal diamond growth. Whether needing the highest purity, NV- centers, colorless, or fancies (pinks and others), this is all possible today.
Production
One can develop the best process in the world, but if it never leaves the laboratory, it does not matter. Exolv understands this fact, and developed a proven mass production process that is capable of meeting your diamond needs.
“You never change things by fighting the existing reality. To change something, build a new model that makes the existing model obsolete.”
― Buckminster Fuller
The DCCVD reactor is a custom design specifically for large volume diamond growth. This is the largest in the industry with unprecedented control over process conditions. It is possible to change power and pressure while keeping temperature constant, unlike competing reactors.
The plasma between DCCVD and microwave plasma CVD (MPCVD) reactors is different, which is readily apparent when looking at the process. MPCVD is a “ball” shape, while DCCVD is a “pancake” shape. This may not seem like a concern, but this leads to different temperatures across the growth surface. For example, from center to edge with MPCVD, which is typically 50 mm total diameter, the temperature is as much as 150°C different. For DCCVD, this difference is around 10°C with a larger growth area of 130 mm.
This is the Exolv system, the future of diamond growth technologies.
Two reactors. Unlimited possibilities.
DC75X
If looking for a research reactor with the widest possible range of process parameters, the 75 mm diameter deposition area is ideal. This provides a quality foundation that is customizable to meet any need.
DC130X
The mass production tool with a 130 mm diameter area, this is the largest in the industry and provides unparalleled control and output in both R&D settings and mass production environments.
The DC130X reactor can hold 180 7x7 mm wafers, compared to 37 wafers for a 50 mm MPCVD reactor. The Exolv reactor is by far the largest in the industry.
The CVD Process
The chemical vapor deposition (CVD) process works by placing diamond wafers (slices of HPHT diamond) into the reactor chamber. Air is removed from this chamber by a vacuum pump and a specialty gas mixture is added, primarily hydrogen and methane. Other gases may help with certain growth and product qualities. Once at the correct pressure, electricity is added through the plasma generator (in this case, a direct current generator), igniting the gases into a plasma. Carbon precipitates from this plasma onto the wafers below, mimicking their structure and resulting in diamond growth.
See below for the Exolv DC130X reactor with a full load of diamond wafers.
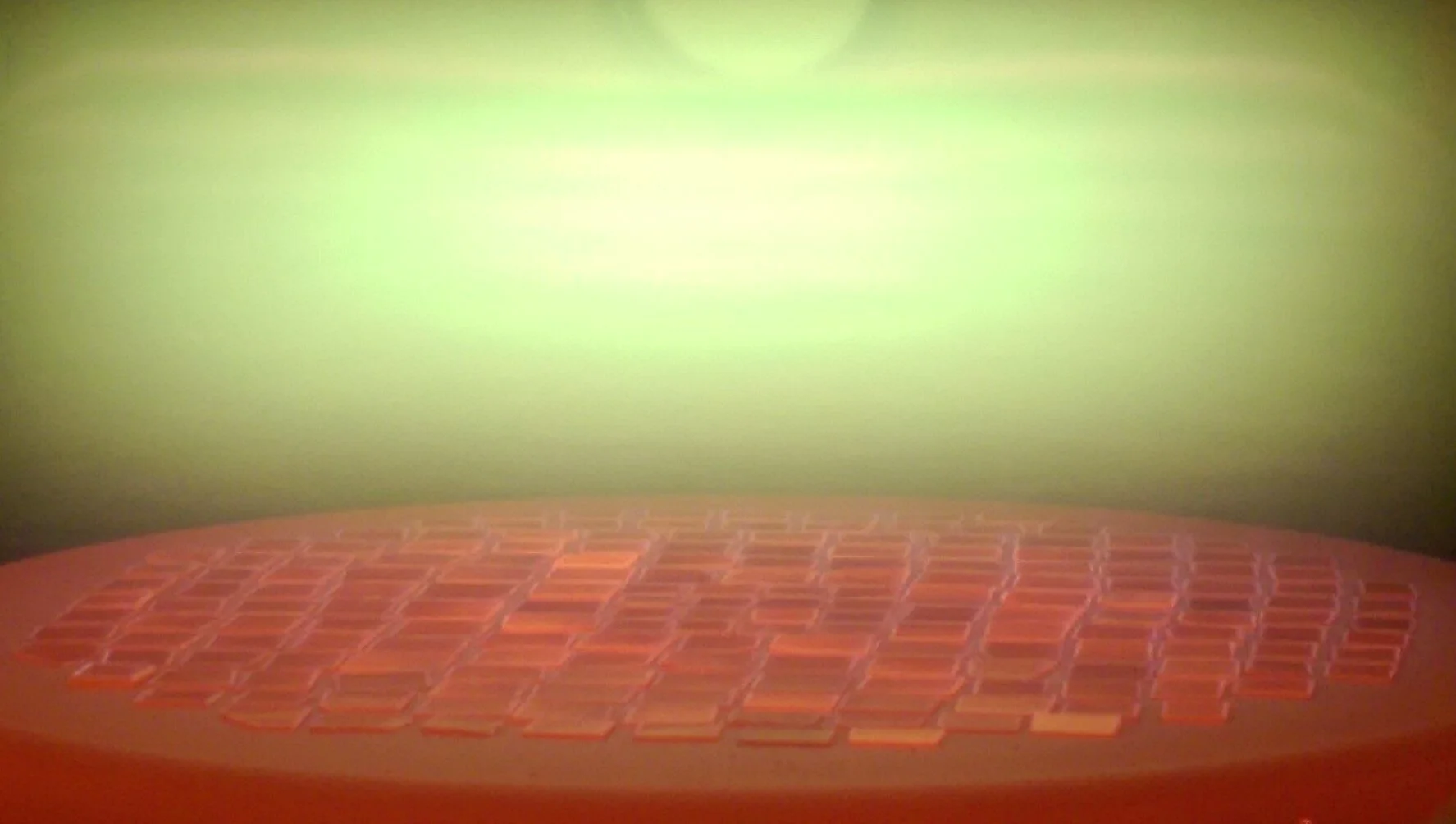
Get in Touch
Reach out today to learn more about how the Exolv DCCVD diamond reactor technology and process can benefit you.